At the end of March 2021, the DCC held its third virtual celebration event where our 10th and 11th cohorts received their Yellow Belt Lean Six Sigma accreditation.
We also celebrated our first two waves of graduates who completed their Green Belt Lean Six Sigma accreditation.
Here at the DCC, the Smart Way Continuous Improvement Yellow Belt and Green Belt courses have been running for the past two and a half years. Originally delivered at face to face workshops, in the last 12 months we have had to be agile and find a different way to deliver the training to our colleagues online in the same engaging way. It was important to us to maintain the development for our colleagues and ensure we provided the same level of quality in the training.
It has evolved over the 12 months online, adapting from full day workshops (which was far too intense) to now running six half day workshops with regular breaks in the sessions.
Our candidates take a real-life problem, within their control, in their day to day work and use the course to learn the PDCA (Plan, Do, Check, Act) format of tools and techniques, run a pilot and drive improvements.
This practical learning benefits both the graduates in terms of how to see problems and tackle them within their daily roles to drive benefits to the business, and to support business improvements.
For example, in our Finance team, 76% of the month end activities were being posted in the last three working days which was causing a great deal of stress and rework that had to be done in a short space of time. This is common amongst many companies.
After going through the Smart Way Lean Six Sigma course of Plan, Do, Check, Act, and using all the tools and techniques, Rebel Walters, the graduate, was able to reduce this down to 44% after pilot one and to 33% after pilot 2. This enabled the business to become more streamlined in it’s month end reporting activities and took a large amount of stress out of the process.
After the project, one of Rebel’s colleagues, Alex Morris, took the upstream process and improved it further using the tools and techniques Rebel had used, enabling the bulk of the work to be done weekly therefore enabling the month end to be closed two hours earlier than normal.
Through the “Next Steps” part of their projects we have also seen more and more opportunities to drive tangible improvements for the business. Taking the time to investigate and understand the problem, uncover root causes and test solutions has helped our graduates stand back from what they think the solution should be – it’s all about having the data and evidence to create a sustainable solution which will actually have an impact on the root causes.
Here are some of our key summary numbers from the training.
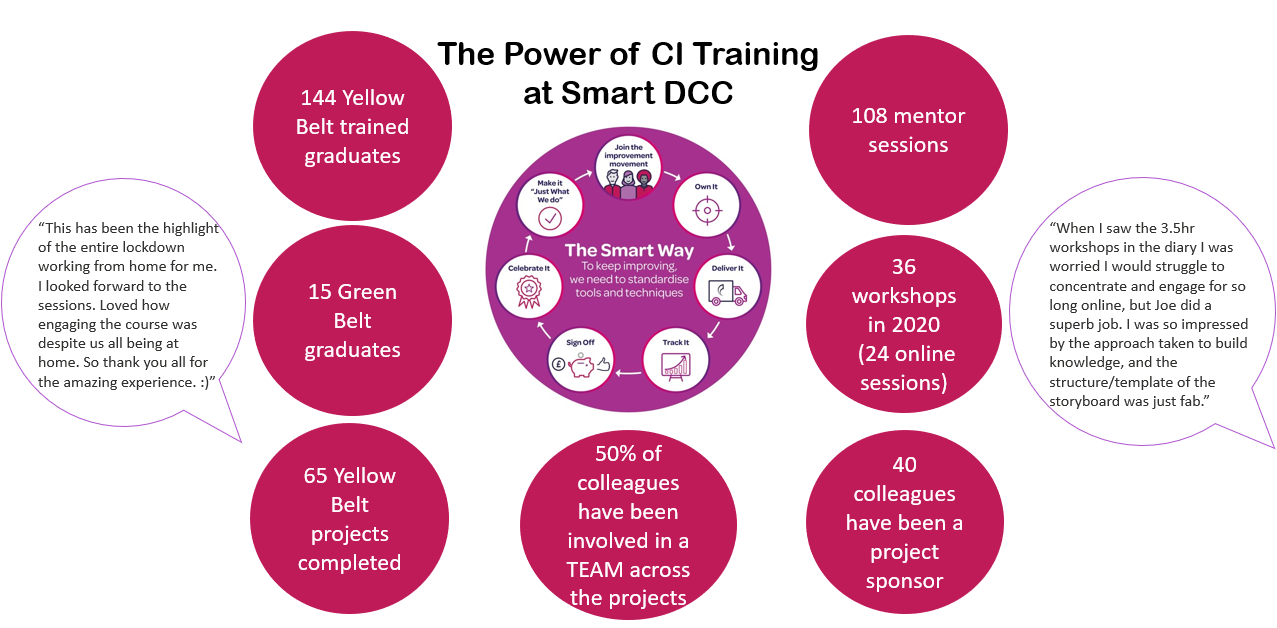
Useful documents
Further reading